.png)
Roeselare site Vanheede becomes more sustainable and efficient
.png)
General contractor Alheembouw is in charge of the execution of the lot closed shell construction and environmental construction. Industrium is collaborating in this project with Architectenbureau Dugardyn, Establis, and Studiebureau Verhaeghe & Partners, within the partnership DEVI. Vanheede Environment Group is assisted by DEVI in the design of the entire site, and in execution takes the lead in coordinating the Techniques lot.
The site on Moorseelsesteenweg will be bordered at the back by a nature reserve and a landfill. Centrally, a new 'Material Recovery Facility' (MRF) will replace existing buildings, allowing the material brought in to be separated into smaller fractions and further material to be recycled. Between this MRF building and the existing PRF will be a new building that will become "the heart" of the site's technical facilities.
Heat grid on site
Compressed air is crucial at the site, including for the sorting and recycling process, to clean areas, and to maintain trucks and forklifts in the workshop next to the MRF. We chose to recover the heat from the water-cooled compressors and send it to the heat grid we are building on the site.
The origin of this private heat grid lies with the 2 CHPs that burn biogas from the landfill at the back of the site, generating electricity. The released heat was made available to a neighboring company and its own workshop. In the future, the heat network will also allow additional heating of the new headquarters, as well as "the heart" of the technical installations, the sorting cabin of the MRF (where manual labor is performed) and the water for the truck washing area.
Reversible cooling
In places where people are working, there is a demand for cooling in the summer. This will be provided by a chiller that runs on electricity and is "reversible" so that it can also produce heat in the winter. This will help fill gaps in heat production that may occur at times when compressed air is not needed - and thus the compressors do not provide heat - and when there is insufficient biogas to feed the CHPs. In that case, the reversible electricity-powered cooling plant is a much more sustainable solution than building a new gas boiler room.
Master Plan
We worked out a master plan for all techniques and utilities. For example, a loop is provided around the site with all basic infrastructure such as high voltage, city water, fiber for data and rainwater. From that loop, it branches off underground to 'nodes': the office building, the CHPs and 'the heart'. This creates a logic of main nodes that are all redundantly connected. This master plan also makes the site future-proof for further expansion.
Buffering and sprinkling
Through the roofs of the numerous buildings on the site, we collect rainwater in a new underground buffer basin. This is used to wash trucks and flush toilets, and to spray water on the waste against dust.
Because fire safety is an important issue in waste handling, infrared sensors at the waste supply ensure fire detection faster than if only smoke is detected. If a fire should still occur, the extensive sprinkler system ensures rapid intervention.
Charging trucks
Electricity at the site comes from the CHPs, among other things, but the building owner also plans to provide PV panels on the roofs for additional production. In addition to charging infrastructure for passenger cars, it is noteworthy that we are also making the necessary provisions to be able to electrically charge trucks in the future.
Want to know more about this project and/or the possibilities to make your project sustainable?
Contact our expert Bart Delgouffe: bart.delgouffe@ingenium.be or call 050 40 45 30
Downloads
Related news items
.png)
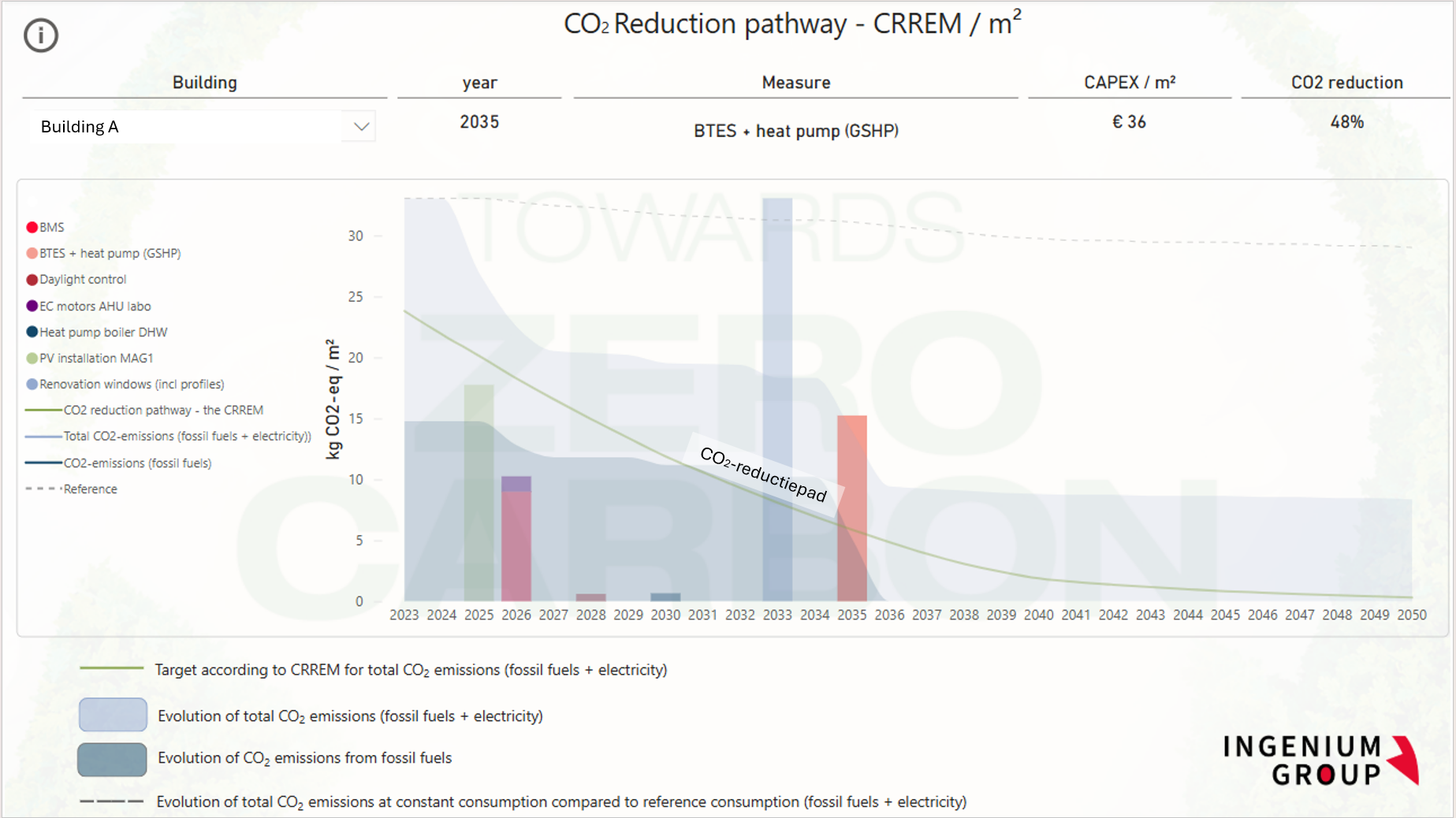
Smart steps to sustainable property management via online tool
.png)