.png)
Retrocommissioning identifies hidden problems (and thus can make money fast!)
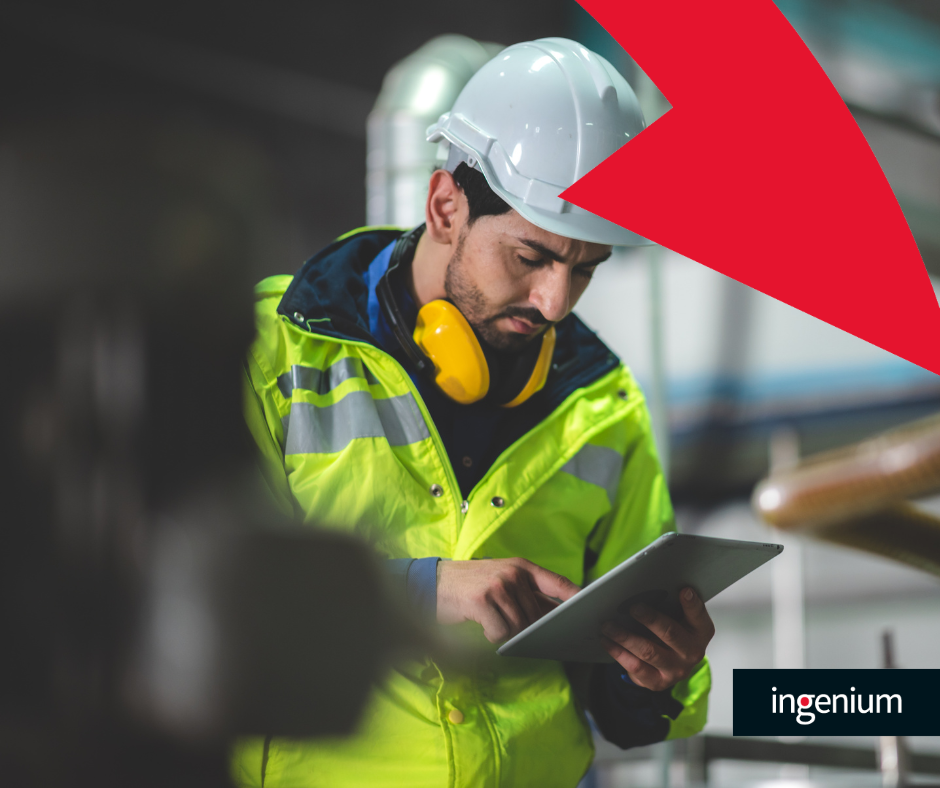
A building management system (BMS) makes life easier for the user/manager of a building. Or at least that should be the intention. However, all too often we see that poorly adjusted installations and BMS result in a lack of comfort and/or considerable energy waste. Through retrocommissioning, we quickly detect hidden causes, provide quick wins and can advise on more sustainable choices for the future.
VARIOUS REASONS
There are several reasons why a lot of building management systems are not or no longer properly adjusted. Upon delivery, it is often checked that all parts of the technical installations are working, but the adjustment of the BMS - which must ensure that everything is in tune with each other and runs optimally - usually only takes place once the building is in use. A different team is often called in for this than at the time of delivery, and the user may already have additional wishes or insights as a result of using the building. If the installations and the BMS have been in use for a number of years, the user or administrator may have changed settings themselves on parts of the installation, without having an adequate understanding of how the whole works, or with insufficient knowledge of the software code - the adjustment - of the BMS. The fact is that technical installations that are not optimally adjusted can result in a decrease in comfort and an undesirable increase in the energy bill.
IMMEDIATELY APPLICABLE
When retrocommissioning existing buildings and installations, we first do a condition measurement and look at the technical concept, current comfort and energy consumption, and how maintenance has been carried out. We make proposals for quick optimizations of the current installations and improvements to (the settings of) the BMS. Our advice and interventions are thus practical and immediately applicable, and deliver quick visible and tangible results. We can also advise which additional control components (taps, probes, meters, etc.) can be used to achieve even more profit. Because by measuring more accurately, the installation can be fine-tuned.
In the next phase, we can look at how an upgrade or renewal of (parts of) the installations and the building envelope can yield further optimizations. On the basis of an energy study, we then determine the final goal, to achieve, for example, a fossil-free or energy-neutral building by 2050 at the latest, via a step-by-step approach. Then we can also concretely work out those adjustments through engineering. And once the new or upgraded installations are operational, we can use seasonal commissioning at the transition to each new season (i.e. every 3 months) to check whether the installations are optimally adjusted or need to be adjusted.
With this approach, Ingenium has a concrete and comprehensive range of services for the entire lifetime of a building or site. The fact that we can draw on over 50 years of experience with installations and BMSs in hundreds of buildings and diverse situations for our advice and designs gives us an edge here over those who manage and/or use only one or a limited number of buildings and installations. Through a combination of commissioning engineers and engineering engineers, Ingenium can test the best practices against current laws and regulations.
CASE
Prior to the retrocommissioning of a customer, we had already been asked to survey all installations, determine their lifespan and draw up a multi-year plan. We were also asked if there were any quick wins. No problems were immediately identified. However, when questioned, comments about comfort did surface. It also emerged that the system - which had been in use for several years - was adjusted manually in various areas during maintenance, but that the BMS was not adjusted every time.
We found about 30 pain points, including:
- In summer, the buildings did not cool sufficiently. This was due, on the one hand, to incorrect heating setpoints, which kicked in on cooler nights anyway, and, on the other, to certain air groups that only circulated indoor air, preventing cooler outdoor air from entering.
- A number of pumps continued to run unnecessarily.
- Because certain control valves were set incorrectly, the indoor temperature fluctuated continuously, without knowing why.
- The legionella treatment had not been adjusted quite correctly, which could lead to long-term health problems.
Re-optimizing and recalibrating the systems and the BMS resulted in that customer saving more than 10 percent on his energy bill in one year. So detecting hidden defects has an immediate positive effect.
Want to know more about retrocommissioning and what its added value can be for your building(s)? Then contact our expert Kenny Vancompernolle: kenny.vancompernolle@ingenium.be - 050 40 45 30.
Downloads
Related news items
.png)
.png)
GRO 2025, the Belgian reference for sustainable buildings is a reality
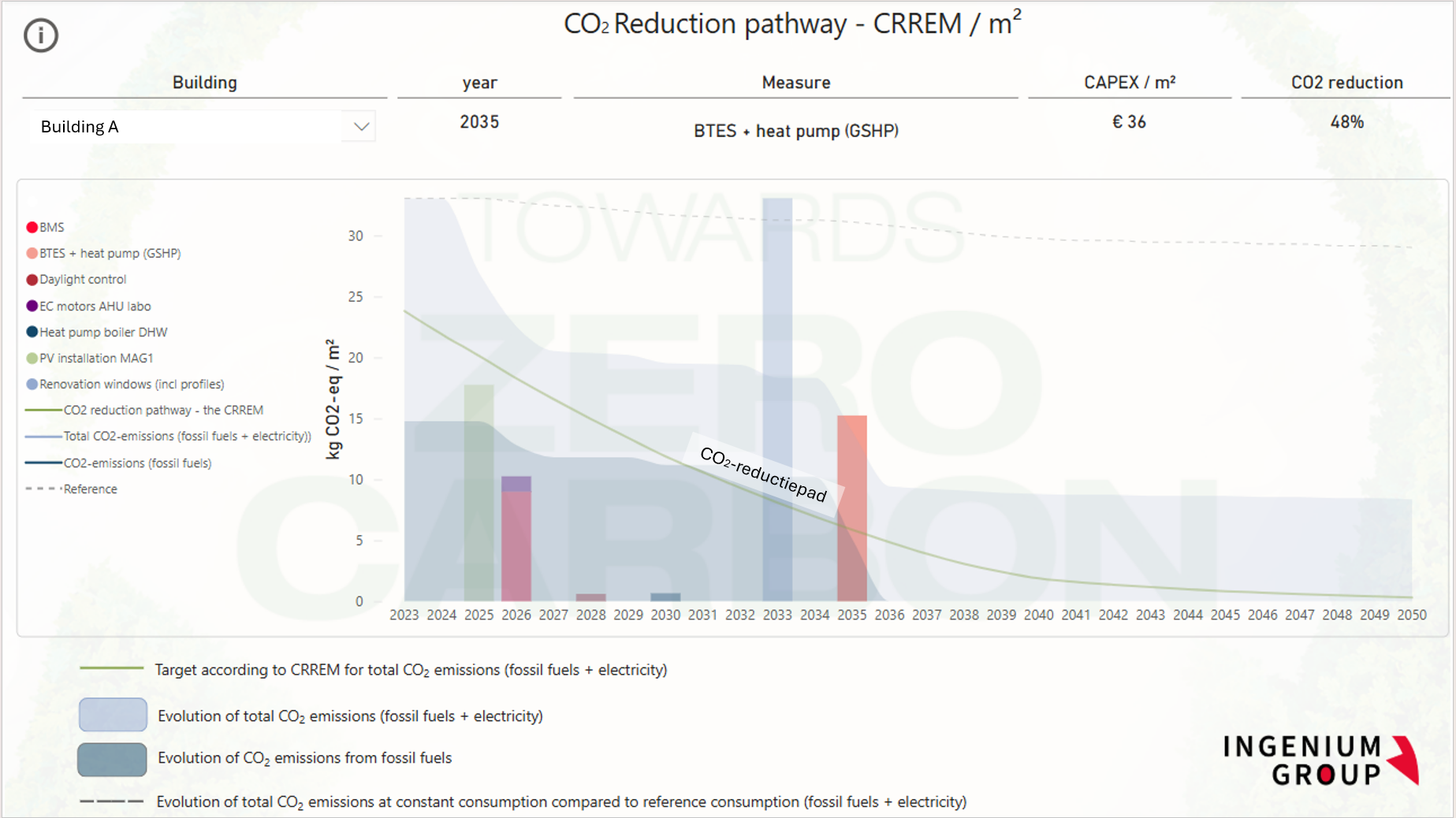