Koen Willemsens
Head of Project Development
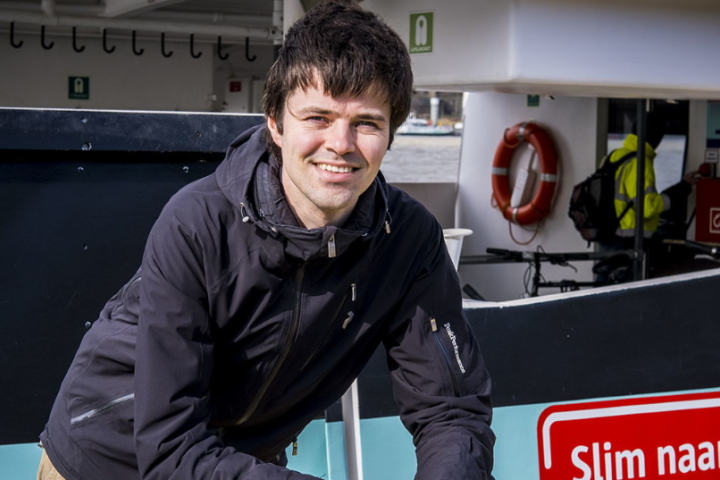
Koen Willemsens has been working for Bopro in Ghent since 2014. Since 2022, he has been head of the project development department there. In recent years he has worked with Ingenium and Industrium in various projects. Bopro focuses on 3 business lines: project management in real estate - 'delegated construction management' - supplemented with all kinds of consultancy and advice, mainly regarding sustainability, since 2014 also developer of new own real estate projects, and finally performance portfolio management of existing real estate on a European scale. Since 2008 Bopro has resolutely drawn the card of sustainability and for BREEAM in use they are even market leader in Europe.
"Typical of Bopro is an integrated approach to projects. We ourselves have a team of 90 people with a lot of expertise, but we like to involve other parties in each project at an early stage for additional insights. That we work a lot with Ingenium/Industrium is because we feel that they not only translate architects' difficult plans into technical installations that fit into those plans, but also really think along proactively to get the most out of a project."
"My first collaboration was at De Stip, the Ghent eco-neighborhood on the old Gantoise sports site with some 150 residential units. We wanted not only flexible and future-proof construction there, but also integrally sustainable:CO2- and energy-neutral, especially as far as the building techniques were concerned. We asked Ingenium: how can we make theCO2-impact of that district lower than what the EPB standard prescribes? They made a feasibility study based on various scenarios related to energy generation and efficiency. The combination of several private building lots around a public domain made it a complex story, especially since we wanted to share the generated energy without having to cross the public domain. The fact that Ingenium was at the table with us at the time and was able to evaluate the scenarios at a high level ensured that we were able to make timely adjustments to the subdivision permit and it did not become a thirteen-in-a-dozen subdivision."
"Since 2017 we have been working together on Blue Gate Antwerp, the climate-neutral business park on the former Petroleum Zuid site in Antwerp. For chemistry dome Essenscia, POM and the City of Antwerp and VITO, we realized incubator Blue Chem with a design & build assignment. Ingenium was part of the winning consortium of MBG, which from the outset strongly committed to thorough studies. Whereas in the first tender round others for techniques came off with'approximately prices' per square meter, Ingenium already had a basic BIM model in which they had already optimized how the techniques would run up to the labs. That gave us a lot of comfort."
"During the same period, we also worked on Blue App, a pre-incubator spin-off of University of Antwerp. There, 50 percent of the construction budget consists of techniques alone. It is therefore a Rolls-Royce of a lab. In both projects, flexibility was very important, because we didn't know in advance who was going to be in the building and how big the units should be. Starting from averages for the techniques, Ingenium made a whole study of how we could then fill that in flexibly later on. UAntwerpen also wanted to test the building thoroughly before it was put into use. Ingenium acted as commissioning agent. The three months before delivery - all works had to be completed by then - were used to intensively test, adjust and approve everything. Digital stress tests were also done in the BIM model using Hysopt so that everything worked as it should by the time of delivery. In the first year in operation, commissioning was then immediately refined season by season. That way of working is where we need to go in the future."
"Ingenium is strongest when they're really conceptually co-foundational. Engineering techniques are often people who say, 'I get a plan from the architect, that's what it is, and I have to draw my techniques in there.' But you don't get optimal results that way. Window openings are drawn too large, requiring many more techniques to compensate for overheating, tubes are drawn too small or impossible curves,... The classical engineer techniques adapts to the challenge. However, we ask Ingenium, "Tell us yourself what is the optimum for you, what you think will work best. When architecture, stabilities techniques are equally matched, we get much further."
"There is a lot of knowledge at Ingenium/Industrium about the various disciplines in terms of techniques. But that is not where they really excel. It is their project engineers who have sufficient knowledge of all those aspects that make the difference. When we ask them what they optimally want in a project, the best comes out. At that moment, they really are the party that is solution-oriented, transparent and reliable in terms of estimates and results. Better to do more at an early stage than to wait until something impossible is on the table and then say it will be difficult to realize. An integral approach from the start ensures that this emerges in good time, and has a lot of added value."
"Since 2021, we have been working with Industrium on the Terminal project at Blue Gate. The basis is a recognizable typology of an industrial hall with column grid of 12 by 12, 48 m deep and 8 m high, with several sheds to rent. Only, to save space, we stack them twice on top of each other, which is unique in Belgium. We started from a white sheet and each discipline made a study of its optimum. Industrium investigated among others for the high voltage the ideal number of transformers, thick and narrow cables, because in a project of 80.000m2 we are quickly talking about many kilometers. The dimension of the technical rooms within that grid was also studied hard. Very important was that we used BREEAM - we are aiming for outstanding - not purely as a label but as a tool to realize a truly sustainable building. By doing thermodynamic studies at a very early stage and going for an integrated approach, it turned out that we could opt for full electrification for heating and cooling, and thus work fossil-free."
"The 5 megawatts of solar panels on the roof of the Terminal project we wanted to maximize local exchange with our tenants. Industrium investigated how we could make a business case out of that, so that in addition to the rental income from the square meters of building, we also have an income from energy. So we were able to make a more performing building. For that we didn't have to drastically increase the rental price, but we were able to convert part of the investments into opex. So in the tender this was broken down: which technologies are in the square meter price and which in the energy business case?"
"I lie awake when I feel a project is derailing, but that is not brought to the surface in a measurable way. As a developer, you are at the table very early on, even before a line has been put on paper. At that moment, based on integral feasibility studies and analyses, knowing all your risks and opportunities well is really essential. You know that what you will eventually build will be something different from those initial plans, but it is very important as the project evolves to know which opportunities you can still keep open or close and what risks are associated with them. And in that, Ingenium/Industrium is a crucial partner for us."
"Typical with Ingenium/Industrium is their scale and breadth of experience. We have already realized labs with them, which is a different segment and class than an industrial hall. But you notice that they come up with realistic solutions in both types of projects. And then we review together of 'where do we do more or where do we do less,' and make adjustments."
"I would describe Ingenium/Industrium's style as 'curious and reliable.' They have enormous knowledge and know what works and what doesn't - hence reliable - but they are also always open to exploring new techniques and possibilities. Moreover, we match because we find that with them, too, sustainability is not an "add-on," but that their entire company is integral to it. Just like with us, it's in their DNA."